目前,通常在家用煉油廠的大多數(shù)減壓裝置中使用的蒸汽系統(tǒng)已被抽成真空,這需要大量的蒸汽用作排空介質(zhì),同時需要大量的酸性水。生成。面對日益嚴格的環(huán)境保護法規(guī),煉油廠需要清理或燃燒這些排放物,這是非常昂貴的選擇。為了節(jié)省蒸汽并降低成本,國外越來越多的煉油廠選擇不需要工作流體的干式真空泵或液環(huán)真空泵,但是它們也存在諸如高故障率和高維護成本的問題。鑒于此問題,國內(nèi)煉油廠認為有必要對煉油廠的減壓設備進行改造。經(jīng)技術人員研究,得出結論:小編提供了真空系統(tǒng)在常壓減壓裝置上的應用。讓我們來分析一下。
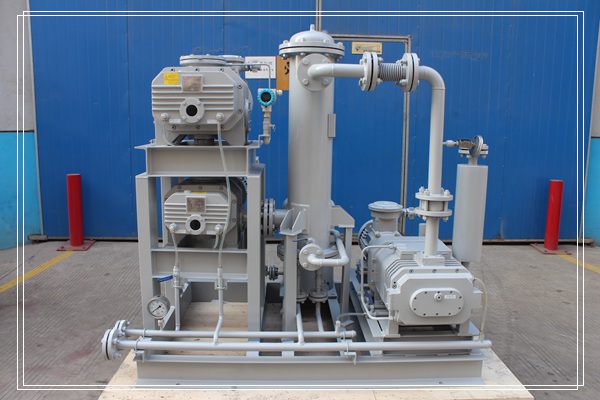
石油煉制行業(yè)的定義
石油:指具有天然性質(zhì)的氣態(tài),液態(tài)和固態(tài)烴的混合物;
原油:指基本類型的石油,在常壓下為液態(tài),還包括液態(tài)非烴類混合物(天然液態(tài)烴混合物);
天然氣:是石油的主要類型,在常溫常壓下呈氣態(tài),在地層條件下可溶于原油。
在燃料式常壓塔和減壓塔的蒸餾過程中,普通常壓蒸餾會切掉直餾汽油煤油,輕柴油,重柴油和其他餾分。這些餾分可以簡單地提煉并摻入合格的產(chǎn)品中。真空蒸餾可削減二次加工原料,例如催化裂化原料,加氫裂化原料等,這些原料經(jīng)過輕量化,精煉和混合后,可生產(chǎn)汽油和柴油產(chǎn)品。這種常壓和真空蒸餾方法已被主要煉油廠采用。因為在常壓塔的進料段中的氣液分離是閃蒸過程,并且在反萃取段中的汽提很難實現(xiàn)輕組分的完全汽化,所以常壓渣油中必須包含柴油殘留物。這些柴油餾出物通過重組分分離,并用作減壓塔中進行二次加工的原料。為了生產(chǎn)合格的產(chǎn)品,需要進行裂化,精制和其他過程。另外,一些柴油餾出物在裂解后變得更輕。汽油,液化氣等。這不僅降低了一次加工中的柴油比例,而且增加了二次加工負荷并增加了單位精煉成本。
目前,我公司針對該問題主要有兩種解決方案:一種是對常壓塔的蒸餾段進行改造。二是減少第一線餾分油返大氣壓塔的精制。由于設備的固有條件限制了大氣塔的蒸餾段的轉(zhuǎn)換,減少一線餾分油精制將不可避免地增加設備的能耗,因此需要重整燃料型壓力還原塔一線還原直接生產(chǎn)柴油成分,效果顯著。
煉油常壓真空裝置專用真空系統(tǒng)具有以下優(yōu)點:
1.不需要水或水蒸氣,減少了能源消耗,大大降低了運營成本;
2,效率高,操作調(diào)節(jié)方便,可根據(jù)生產(chǎn)需要調(diào)節(jié)真空度;
3.可以提高設備的處理能力;它可以實現(xiàn)高壓縮比和高達25MPa的排出壓力;
4.無需大面積冷凝器,節(jié)省能源,安裝方便;
5,無酸性水排放,減少環(huán)境污染;
6.使用負一線油作為介質(zhì),以節(jié)省資源。
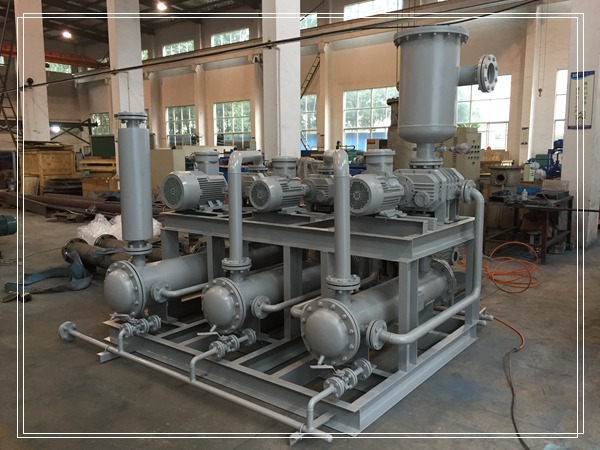
通過對傳統(tǒng)煉油常壓減壓裝置的分析,并結合改進的煉油常壓減壓裝置的效果,可以了解到真空系統(tǒng)在煉油常壓減壓裝置中的應用煉油廠生產(chǎn)速度,能耗和成本起著重要作用。